Optical system with aluminium reflectors
The optical system proposed by AEC is called HIGH PERFORMANCE OPTIC and is based on a LED module on which a highly efficient aluminium reflector optic is mounted. LED module and optics are constantly protected by a flat tempered glass with high transparency.
The AEC reflectors, on the other hand, have been tested according to DIN EN 16268 for long-term material stability, achieving an A+ classification after accelerated ageing tests.
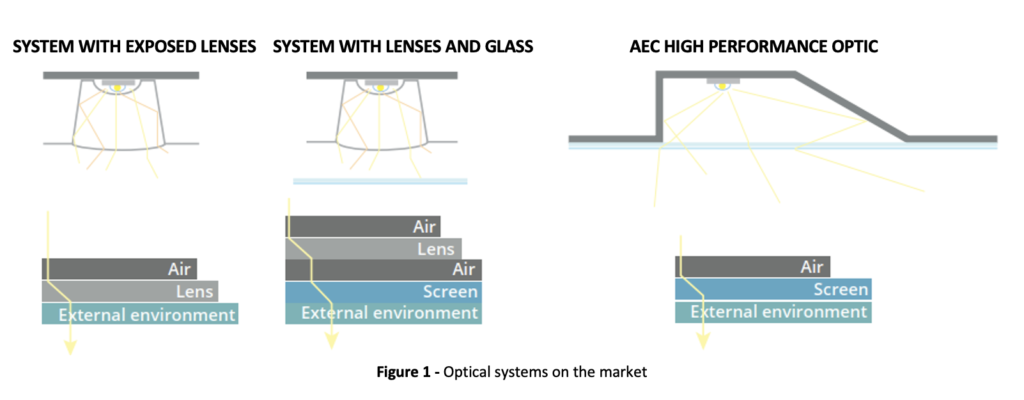
Optical systems with plastic lenses
In the case of optical systems consisting of LEDs and plastic lenses, the latter are in direct contact with the light source and are directly and constantly exposed to the effects of ultraviolet radiation, humidity and thermal cycles typical of an outdoor luminaire. These effects, although reduced, are also present when the optical unit is protected by a protective glass.
Although PMMA optical lenses have good optical properties, they have a glass transition temperature Tg of up to 80°C. The glass transition temperature is the temperature at which an amorphous polymer changes from a hard/glassy to a soft/rough state or vice versa. The Tg is directly related to the strength and capabilities of a material in a given end application. Once this temperature has been exceeded, the material starts to deform and the optics can change its shape, resulting in a change in photometry geometry.
Optical lenses made of polycarbonate, on the other hand, have a higher glass transition temperature Tg than those made of PMMA and other polymers, which therefore allows for greater resistance, however, this material is strongly subject to UV radiation, which causes yellowing and ageing of the material. This process is accelerated by high temperatures, so that despite the material’s greater resistance, it is important to keep the material’s service temperature below specific limits, for example, by limiting the power of the luminaire appropriately. Such yellowing results in a loss of output flux compared to what was initially assumed, which is then added to the normal depreciation of the LED’s luminous flux. UV- and heat-dependent yellowing also does not occur homogeneously on the lens, so in addition to the possible loss of flux there is also a potential change to the photometry and thus also to the uniformity parameters.
For both solutions, it is also important to check that the adhesive materials for construction or attachment are compatible with the plastic lenses used, otherwise short- and long-term degradation may occur. Inappropriate use or exposure to solvents is also something that must be taken into account as it can cause rapid degradation, attacking the plastic structure of the material.
Accelerated tests on typical lighting plastics have also led to results showing colour change, permanent deformation of the lens and thus of the photometric solid, opacification and even breakage.
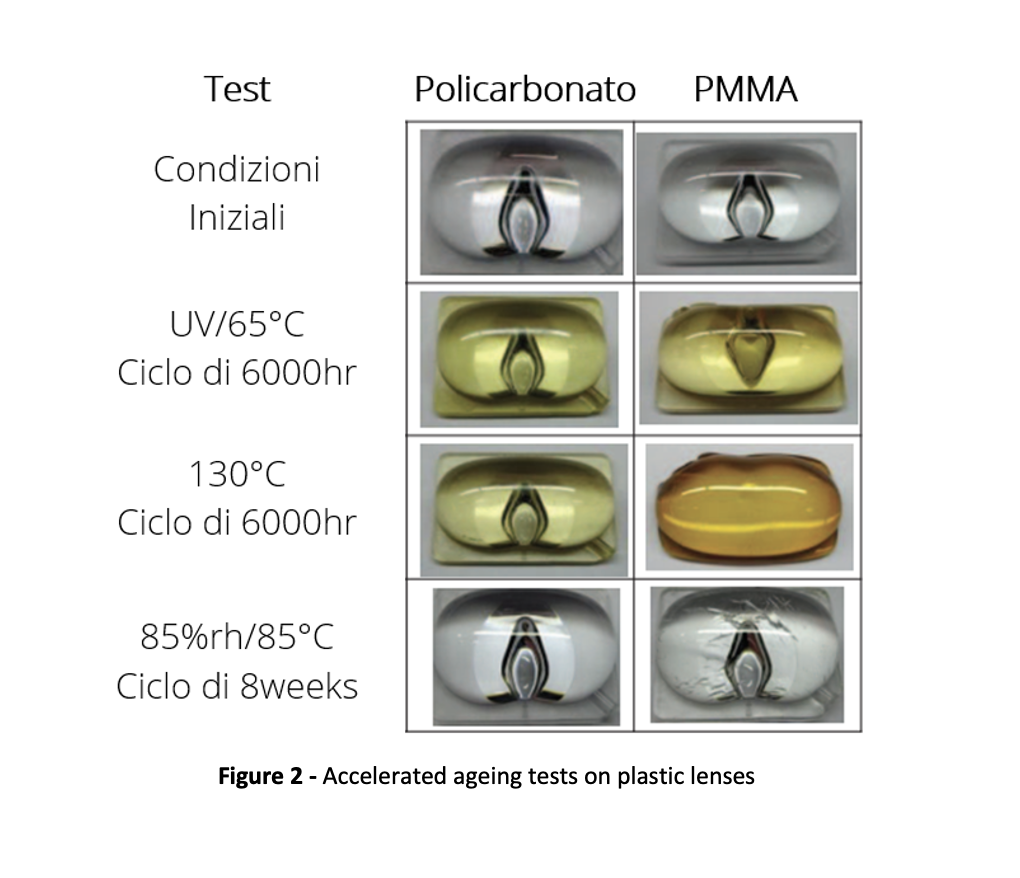
A study campaign on material degradation promoted by the French lighting association AFE (Association Francaise de l’Eclairage) led to the following results :
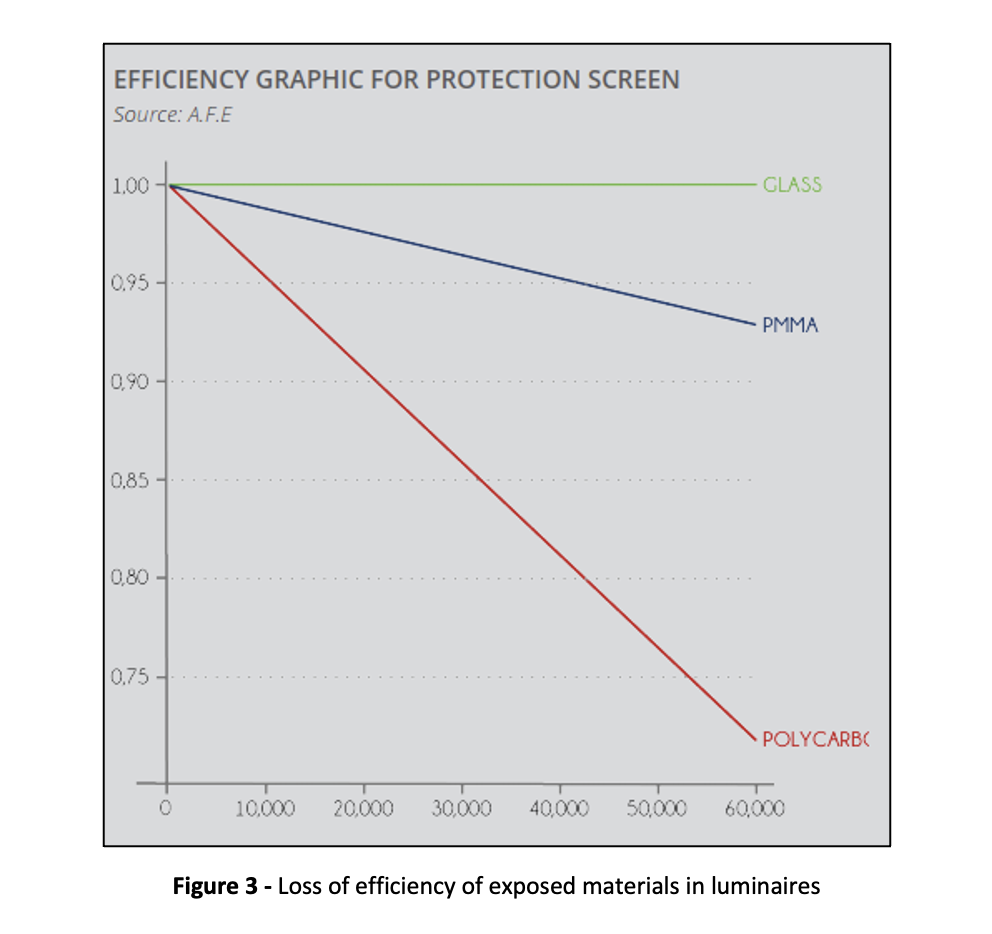
It can be seen that while glass (once cleaned) returns to its original efficiency, materials such as polycarbonate and PMMA degrade irreversibly and even if cleaned, show a permanent loss of efficiency already after a few thousand hours.
Finally, the results of tests carried out by the University of Antwerp (Belgium) in a TUNNEL installation where luminaires with lenses and with glass were installed without being powered to assess the impact of the road environment on the exposed materials. A comparison of performance between the first day of installation and after only three months in the tunnel is shown:
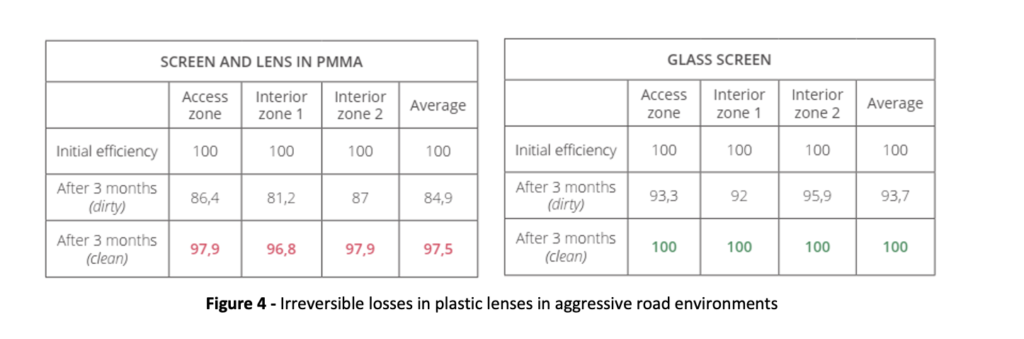
Plastic materials are irreversibly compromised after only 3 months (2.5% loss of efficiency in 3 months, estimated loss of more than 50% in 50,000hr), while glass retains its properties even in harsh road environments. In conclusion, therefore, an optical unit built using aluminium reflectors protected by tempered glass is a more valuable and durable system than one with plastic lenses. The two technologies could only be considered equivalent (in terms of service life) if the optical lenses are also made of glass and not plastic.
Conformity to specification
The optical modules installed inside AEC Illuminazione’s luminaires fully comply with the requirements imposed by the document ” Requerimientos técnicos exigibles para luminarias con tecnología LED de alumbrado exterior ” in chapter 5, paragraph 5.1, as
- The photometric engine is based on a PCB system that uses the principle of photometric addition using several LED light sources.
- Each optical module consists of several light sources and each module will generate the required photometric distribution.
- Despite the fact that each LED is required to be associated with a lens, the LEDs themselves within the module are driven at very low currents with a failure rate of less than 0.01% at 100,000 khrs, so failures that could cause the photometry to change from its initial conditions are almost non-existent.
Furthermore, degradation of the optics due to temperature is not present in luminaires equipped with AEC High Performance Optics, where the aluminium reflectors (a material specifically used in optical applications) are not affected over time by the effect of ultraviolet radiation (partially shielded by glass), humidity and daily thermal cycles. The materials used in the manufacture of the optical reflectors have also been tested to ensure maximum performance throughout the life of the product. A loss of reflector efficiency of no more than 1% is estimated after 80,000hrs of operation.
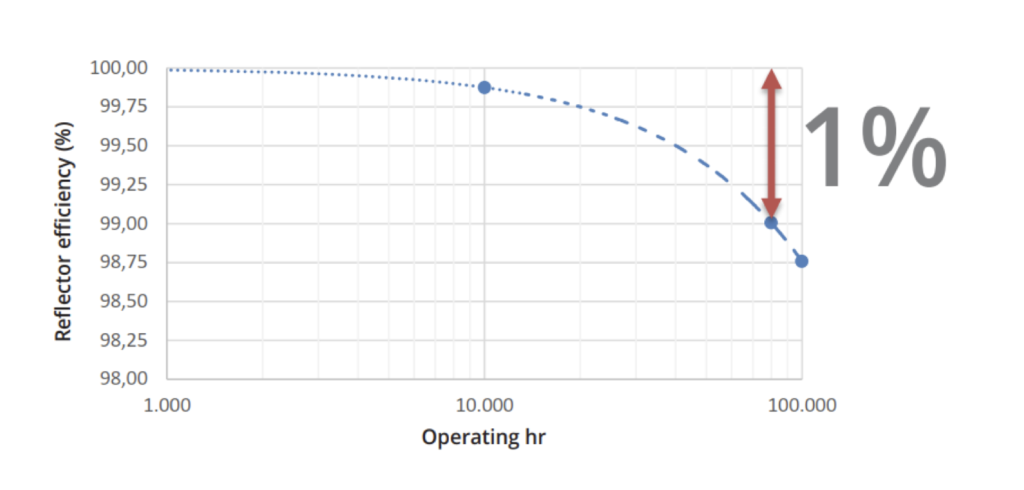
The AEC High performance optic system was designed precisely with the intention of exploiting the efficiency and optical qualities of LEDs and at the same time maintaining these qualities throughout the life of the luminaire, aware of the sometimes harsh conditions to which luminaires are exposed.
Compared to classical solutions based on plastic lenses, which are subject to ageing and permanent degradation, AEC’s proposal, especially in the LCC (life-cycle-cost) vision, is better in terms of optical performance and reduction of energy consumption.
Color angular uniformity
The LED module system with an aluminium reflector guarantees superior light quality, with angular colour uniformity superior to that of individual plastic lenses on individual LED chips. An image of the above phenomenon is shown below as an example.
Colour angular uniformity is a qualitative phenomenon of light, referred to in the ENERGY STAR® Program Requirements for Lamps.
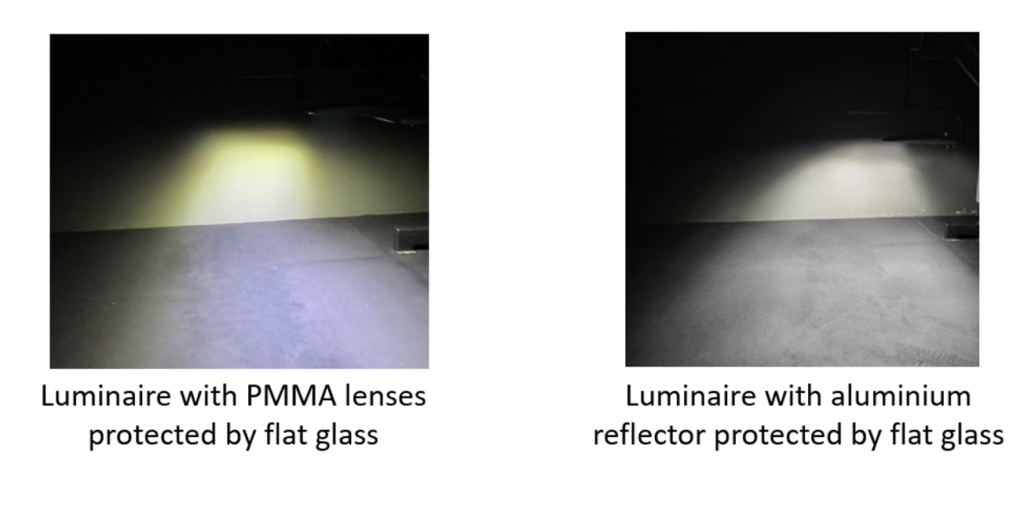
Normative references
Aluminium reflector technology is widely appreciated by public authorities worldwide such as:
- New Zealand Road Administration ” TDM-SL_04_App-B2_LED Roadway Lighting – Luminaire Assessment Checklist_v20_2021-01-15 “, where the equal use of glass-protected aluminium reflectors and glass-protected PMMA lenses is permitted.
- Standard ASNZS1158.3.1-2020, APPENDIX E permits the use of both optical modules consisting of single LED lenses and LED modules with aluminium reflectors.
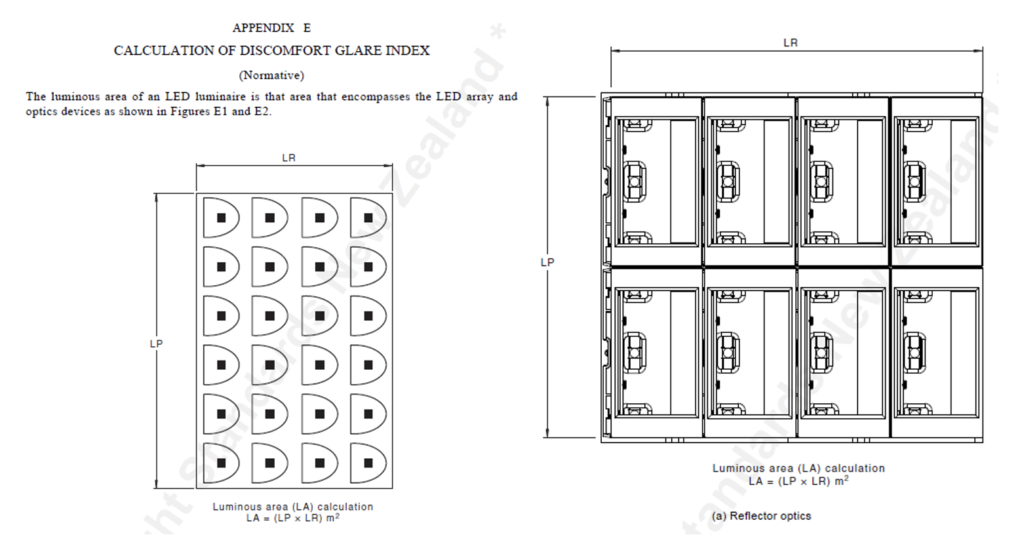
- Technical specification “ NMF01:2021 LED luminaires – requirements “ scandinavian countries. The specification permits the use of both optical modules consisting of single LED lenses and LED modules with aluminium reflectors.
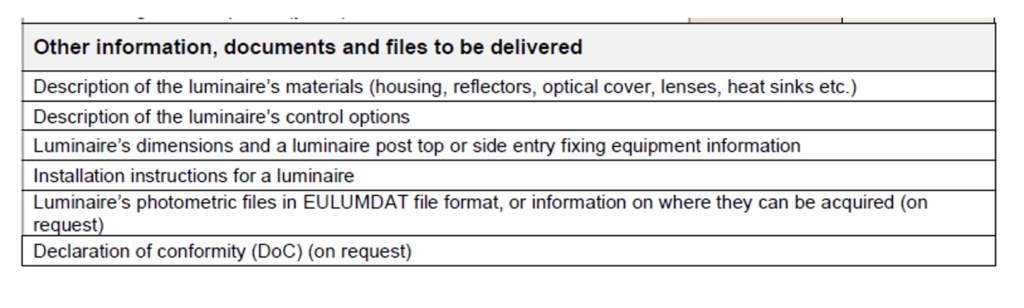
- Technical specification “Road Lighting & Electrical Installation” in Oman where the use of plastic lenses is only allowed under certain conditions to be demonstrated (page 15-36), extract below.
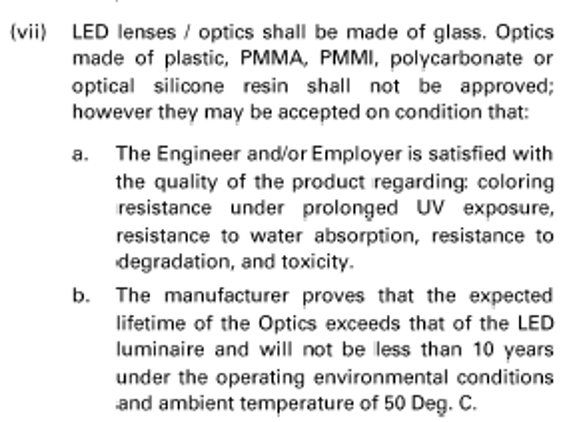